
En janvier dernier, celle qui se faisait autrefois appelée MBK Industrie S.A.S a connu un changement hautement symbolique en délaissant son patronyme par celui de Yamaha Motor Manufacturing Europe S.A.S. Descendante de Motobécane – passé sous le giron du géant japonais en 1986 -, cette usine française située à Saint-Quentin, dans l’Aisne (02), a décidé d’épouser la grande tendance de notre ère, celle de l’électrique.
Historiquement, l’usine est le lieu de conception de scooters et motos thermiques bien connus : les motos Ténéré 700 et MT-125 par exemple, mais aussi le best-seller de la marque nipponne, le fameux XMAX. En cette année 2024, le groupe ajuste son tir en mettant en place une toute nouvelle ligne de production dédiée aux moteurs pour vélo électrique.
Une ligne jumelle du Japon
En réalité, un seul et unique moteur est pour l’instant produit : le PW-S2, lancé en septembre 2022. Il s’agit ici d’une ligne jumelle japonaise, directement « importée » de la maison-mère avec des « ajustements plus pointus en matière de sécurité », afin de coller aux normes européennes, nous explique un représentant de Yamaha France.
Pour la déployer, « nous sommes allés au Japon, nous avons eu des formations de maintenance, de qualité et de développement », nous explique notre interlocuteur. À l’avenir, d’autres moteurs pourront être produits sur cette ligne de production, laquelle est compatible avec d’autres systèmes et bancs d’inspection.
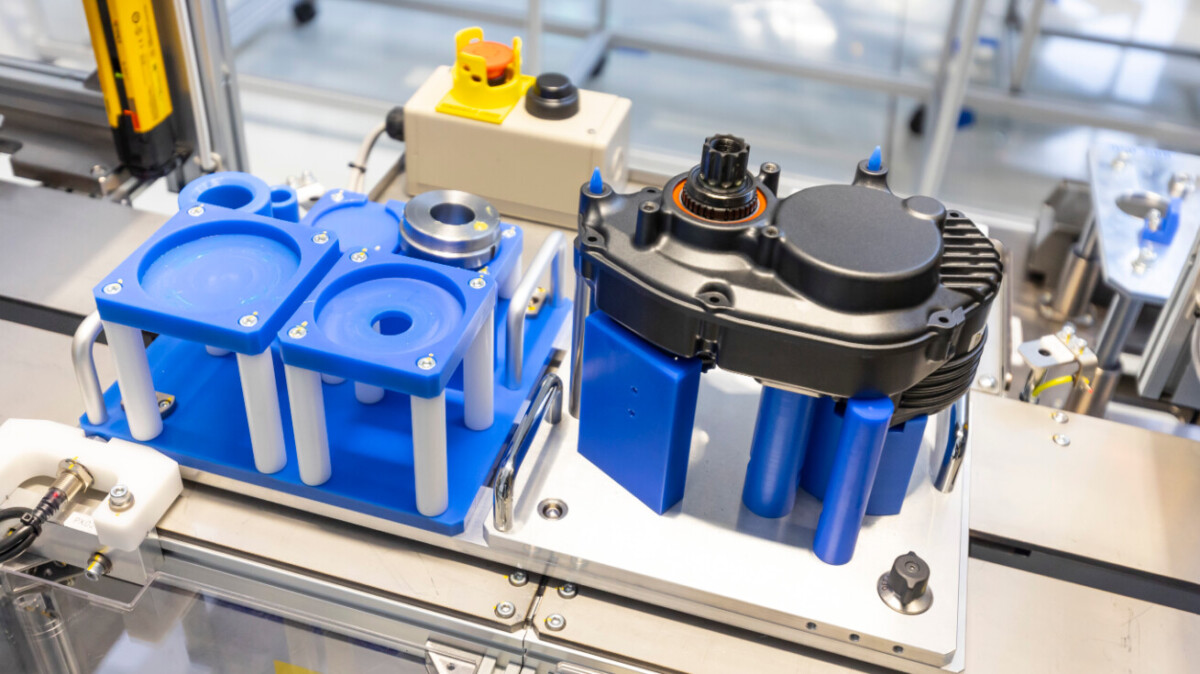
Plus concrètement, comment fonctionne cette fameuse ligne ? Les pièces sont tout d’abord organisées par chariot puis emmenées sur une ligne dite de préparation. Ici, des sous-ensembles composés des pièces sont assemblés sur des racks dynamiques par des opérateurs. « Il s’agit des engrenages, des roulements, on prépare les mécaniques du moteur avant de les assembler », nous explique-t-on.
Ce petit manège permet de créer des kits et de valider la présence de toutes les pièces montées. Le tout se dirige ensuite vers une ligne de convoyage composée de 6 postes de travail. « On a des détrompeurs qui valident chaque opération, pour savoir si tout est conçu dans le bon ordre, avec les bons paramètres, et d’autoriser le mouvement vers l’opération suivante ».
Des vérifications, tout le temps et partout
Yamaha met un point d’honneur à littéralement tout vérifier, pour minimiser les marges d’erreur. « Le travail est 100 % manuel, la machine est surtout là pour contrôler ». C’est ici la politique du groupe, qui applique les mêmes méthodes au Japon et en France.
Durant le processus, les pièces et sous-ensembles sont démagnétisés, « car il peut y avoir de l’électricité statique » que certains systèmes n’apprécient guère. Cela peut notamment impacter le capteur de couple, qui a besoin d’être coupé du champ magnétique au risque de devenir non fonctionnel.
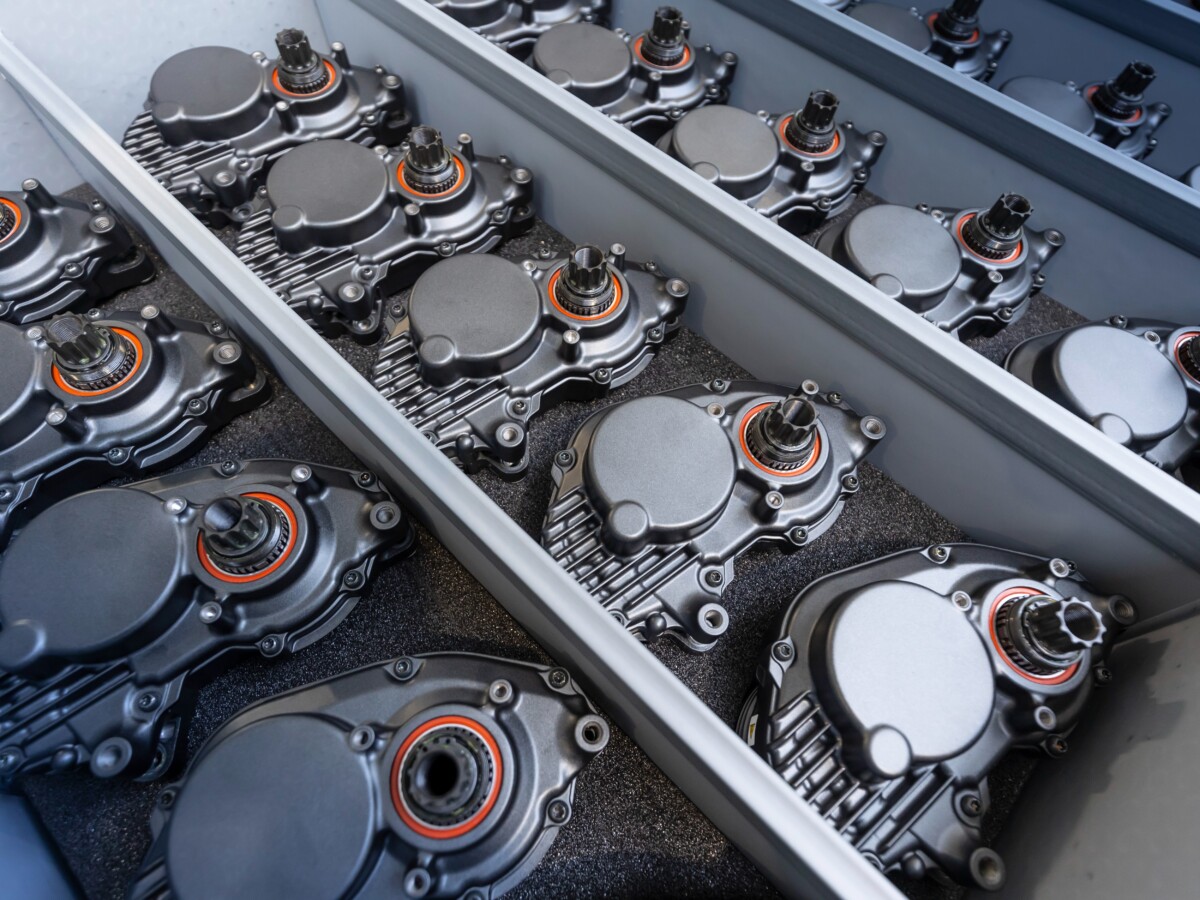
En bout de ligne, un système robotisé se charge d’appliquer des joints pour garantir l’étanchéité du moteur. Une énième vérification par caméra cette fois-ci contrôle l’ensemble du moteur avec de l’imagerie. Yamaha a préféré rester discret sur le nombre de contrôles effectués. « Ce qui est nécessaire », nous a-t-on simplement indiqué.
Enfin, le moteur est soumis à un banc d’inspection : ici, une machine va entrer dans les paramètres du moteur pour contrôler sa qualité, le calibrer, comprendre dans quel angle il travaille et valider les performances. C’est un contrôle qualifié de très sévère et poussé, qui permet en outre de tracer le produit dans ses moindres détails.
Des stocks de sécurité
L’étape finale consiste à poser le carter du moteur, qui est ensuite stocké dans un rack avec un de temps de séchage là aussi contrôlé – un peu moins d’une demi-heure. La première pièce moteur produite est la première à être utilisée, pour bien respecter les temps de séchage. Une fois le moteur fini, il est expédié dans des boîtes retournables qui font des allers-retours entre Yamaha et le client.
En cas de problème sur une pièce, la firme nipponne l’identifie, la change et l’enregistre pour savoir de quel lot elle provient. Sans grande surprise, Yamaha dispose d’un stock de sécurité pour pallier ce type de problème. Plus globalement, le groupe s’assure un stock de moteurs pour n’avoir aucune contrainte vis-à-vis d’un client, quitte à avoir un poil de surtockage.
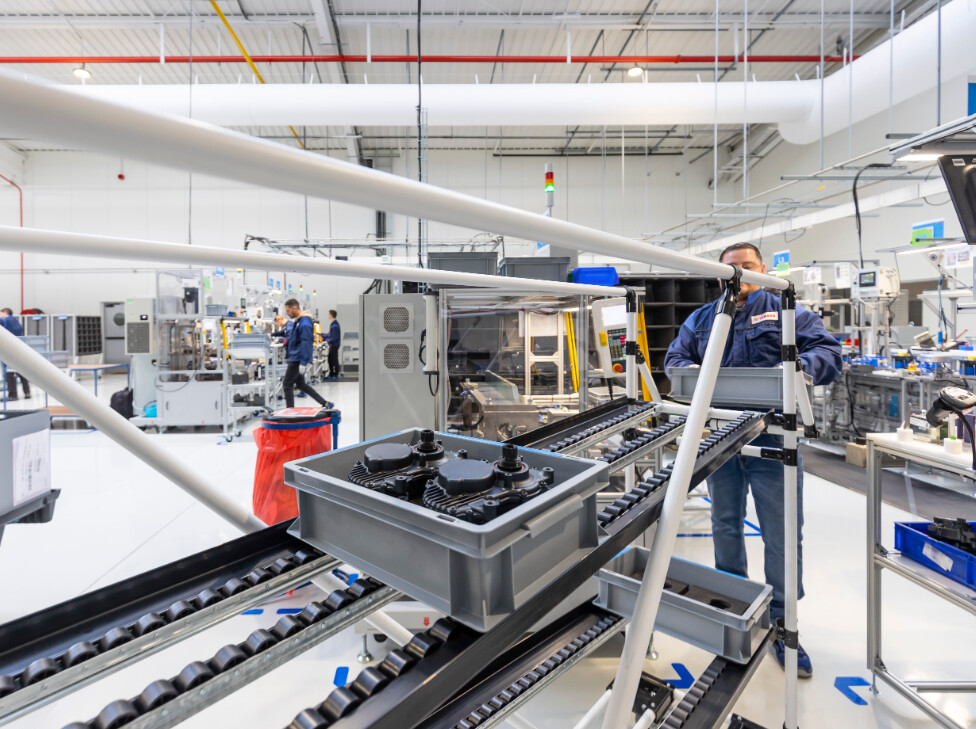
Au total, chaque moteur compte environ 60 pièces, avec plusieurs sous-ensembles directement envoyés du Japon. Cette ligne de production fait appel à une quinzaine d’opérateurs en permanence : chacun d’eux peut tenir tous les postes (un poste nécessite une journée de formation), nous assure-t-on. Cela permet de développer leur polyvalence, d’éviter les troubles musculaires dus à une seule et même tâche et de multiplier les compétences.
Un moteur toutes les minutes
Une équipe de 15 personnes parvient à sortir un moteur toutes les minutes. Entre ses débuts sur la ligne de production et la toute fin, un moteur met environ 20 minutes à être conçu. Au total, l’usine est en mesure de sortir 100 000 moteurs par an, par équipe, si la ligne tourne 24h sur 24. À terme, Yamaha souhaite ajouter deux autres équipes supplémentaires.
Pour aller plus loin
On a visité une usine de vélos électriques : plongez dans les coulisses de l’industrie
D’ici quelques jours – article écrit le 29 mars -, un premier lot de moteurs sera livré au client dans un camion contenant… 4 500 unités motrices. Le client principal de Yamaha est d’ailleurs bien connu : il s’agit d’Accell Group (Winora, Babboe, Haybike, Lapierre), n° 1 du vélo en Europe qui traverse actuellement une crise profonde (dette, délocalisation, problème technique et rappels).
Ce contenu est bloqué car vous n'avez pas accepté les cookies et autres traceurs. Ce contenu est fourni par Disqus.
Pour pouvoir le visualiser, vous devez accepter l'usage étant opéré par Disqus avec vos données qui pourront être utilisées pour les finalités suivantes : vous permettre de visualiser et de partager des contenus avec des médias sociaux, favoriser le développement et l'amélioration des produits d'Humanoid et de ses partenaires, vous afficher des publicités personnalisées par rapport à votre profil et activité, vous définir un profil publicitaire personnalisé, mesurer la performance des publicités et du contenu de ce site et mesurer l'audience de ce site (en savoir plus)
En cliquant sur « J’accepte tout », vous consentez aux finalités susmentionnées pour l’ensemble des cookies et autres traceurs déposés par Humanoid et ses partenaires.
Vous gardez la possibilité de retirer votre consentement à tout moment. Pour plus d’informations, nous vous invitons à prendre connaissance de notre Politique cookies.
Gérer mes choix