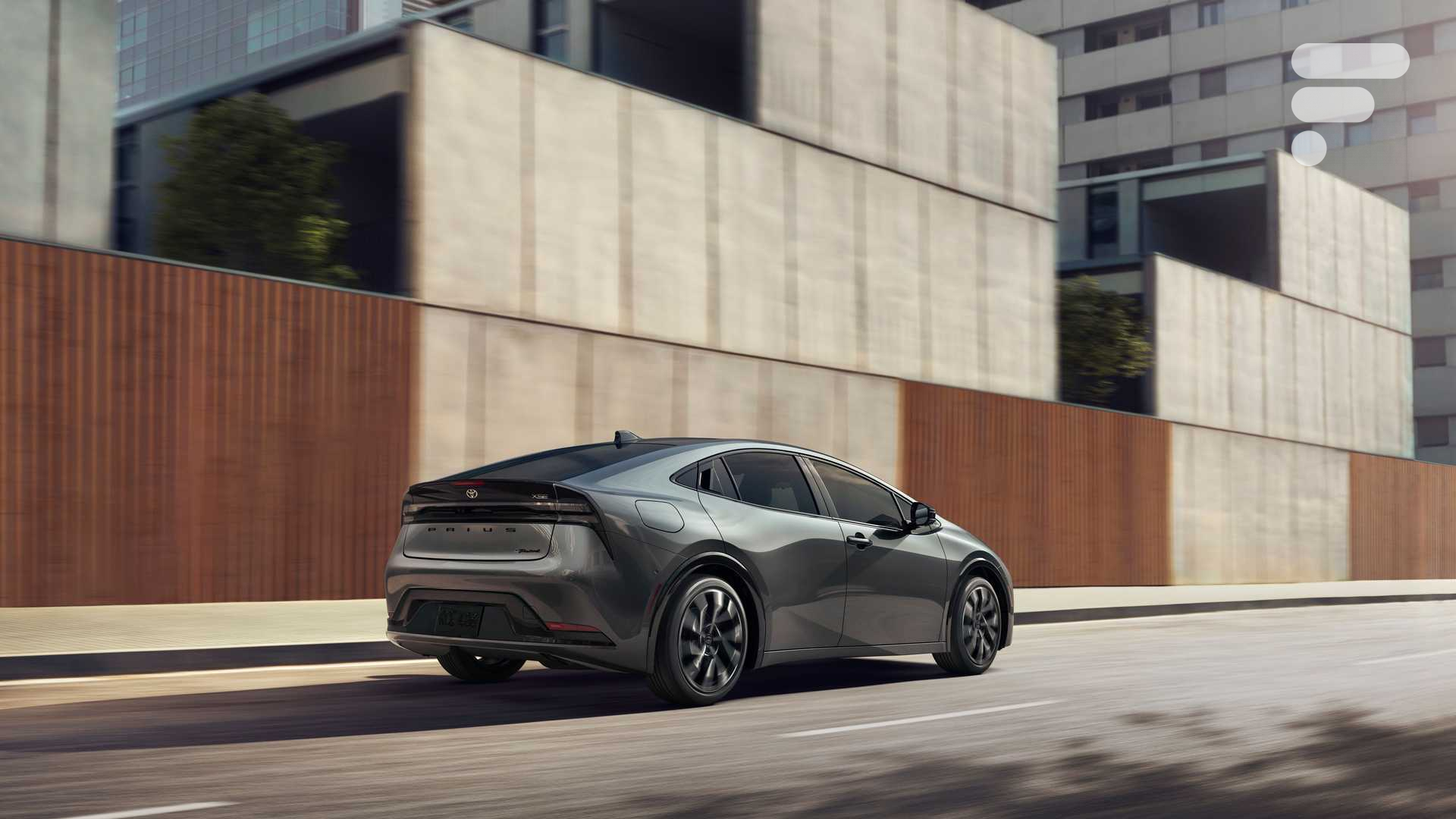
De plus en plus, Toyota fait parler de lui sur le sujet de la voiture électrique. Il faut dire que le premier constructeur automobile mondial en 2022 (10,5 millions de véhicules vendus) a pris un retard certain en matière de véhicules 100 % électriques. Lui qui a pourtant été le pionnier de l’électrification avec ses voitures hybrides et hybrides rechargeables.
Désormais, il est n’est plus question de perdre davantage de temps. C’est même plutôt le contraire : il faut prendre le TGV en marche (ou plutôt le Shikansen) et vite se réinventer pour rattraper les meilleurs. Avec évidemment Tesla dans le viseur. Il faut vite oublier les 24 400 voitures électriques vendues l’an dernier et se mettre en marche pour atteindre 1,5 million de ventes électriques d’ici 2026, et même 3,5 millions à horizon 2030.
Une production entièrement repensée
Et tout ça passe notamment par une refonte complète du process de production. On sait d’ailleurs depuis quelques mois déjà que Toyota va reprendre à son compte l’une des solutions du géant américain Tesla dans le processus de production de ses véhicules : la Giga Press. Mais c’est loin d’être tout. Et le géant japonais prévoit de diviser par deux le temps de production et de réduire les coûts d’équipement de 25 % grâce à la numérisation.
Mais alors comment Toyota compte-t-il s’y prendre pour arriver à la voiture zéro émission avec 1200 kilomètres d’autonomie et la recharge éclair ? Dans un entretien à Automotive News, Akihisa Shiaro en charge de cette révolution de la production électrique chez Toyota a dévoilé plus en détail le plan.
Modélisation 3D et Giga Press
Avant que les nouveaux modèles 100 % électriques Toyota voient le jour, il faut penser la manière dont ils seront produits. Et afin de penser aux nouveaux équipements d’assemblage nécessaires, Toyota va adopter la technologie « digital twin« , une sorte de jumeau numérique de l’équipement qui produira effectivement la voiture. Grâce à un moniteur de 150 pouces et à un logiciel extrêmement puissant, il est désormais possible de penser le plus précisément possible, au millimètre près, la future machine de production. La réalité virtuelle s’invite également dans le processus, permettant aux ingénieurs d’adapter l’équipement aux futures pièces qui seront produites, mais aussi dans le but d’optimiser au maximum la ligne d’assemblage.
Le passage du virtuel au réel permet ensuite d’optimiser les gestes des ouvriers, et parfois aussi de créer des machines pour automatiser certaines tâches et gagner en productivité.
Une productivité qui s’optimisera en réduisant le nombre de pièces dans l’assemblage des futurs modèles. Comme déjà expliqué en juin dernier, c’est là en s’inspirant de la Giga Press de Tesla qui permet de mouler des pièces de carrosserie bien plus grande. Le but de Toyota étant de produire une voiture en trois partie avec l’avant, le centre et l’arrière.
La batterie solide dans les starting-blocks
Que serait une voiture électrique sans ses batteries ? Quand on sait à quel point elles sont importantes dans le prix global d’une voiture, on comprend qu’elles soient là aussi au centre des attentions de Toyota. En l’occurrence, dans son usine de Teiho, le constructeur réalise ses prototypes de cellules et de packs de batteries de nouvelle génération. On parle là notamment de la batterie à état solide.
Avec plus d’autonomie et sa recharge plus rapide, elle serait prête à être industrialisée et commercialisée chez Toyota dès 2027-2028. Et la production de masse nécessite là aussi d’être entièrement repensée afin de ne pas endommager les matériaux très sensibles qui les constituent lors de l’assemblage. Vitesse d’assemblage et alignement sont ainsi optimisés. On parle alors d’une autonomie de 1 200 km (sur le cycle d’homologation WLTP) et une recharge en 10 minutes seulement !
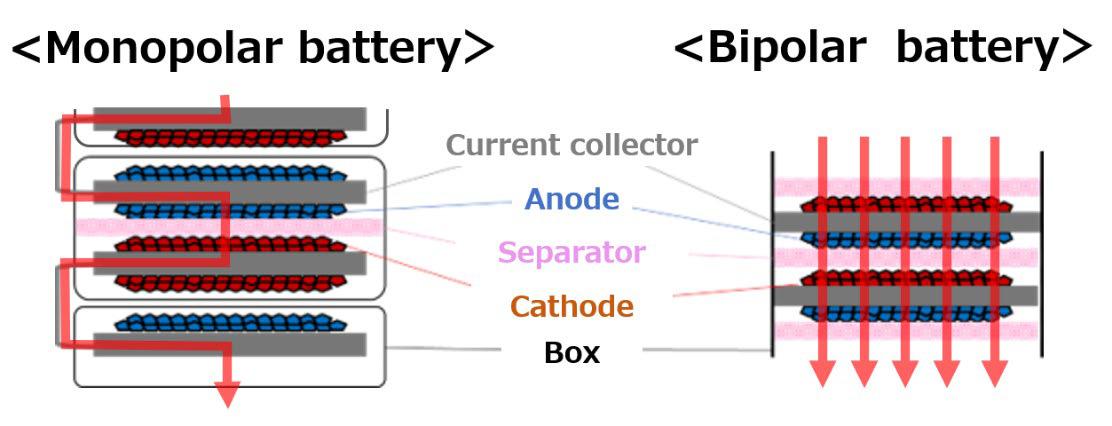
Et puis la chimie elle-même a été repensée et simplifiée avec une configuration bipolaire qui ne nécessite qu’un tiers des composants. Quand dans les batteries classiques, les collecteurs de courant individuels sont revêtus d’une anode ou d’une cathode, un collecteur de chaque étant apparié pour former un ensemble, dans la configuration bipolaire, chaque collecteur de courant est recouvert d’une anode et d’une cathode sur des faces opposées.
Et Toyota de réduire également le prix des batteries en utilisant la technologie LFP sur ses batteries bipolaires au lieu de matériaux rares comme le nickel et le cobalt. L’autonomie de cette batterie dépassera 600 km, soit une augmentation de 20 % par rapport à la batterie lithium-ion actuelle du SUV bZ4X, tout en réduisant le coût de 40 % grâce à une chimie moins onéreuse.
Des voitures autonomes avant d’être sur la route
Toujours afin d’optimiser le processus de production de ses futures voitures électriques, Toyota regarde du côté de la carrosserie et cherche à réduire au maximum les soudures sur la voiture. De plus, avec les différents modèles réalisés grâce à la « Giga Press », les ouvriers peuvent plus facilement insérer des pièces et des composants avant que les modules ne soient soudés ensemble.
Pour ce qui est de la peinture, le constructeur nippon espère réduire l’utilisation de peinture de 15 % et les coûts de 10 %, en plus d’une réduction de 17 % des émissions de dioxyde de carbone.
Enfin, lors de l’étape finale, Toyota souhaite abandonner les chaînes de montage ancrées, coûteuses et peu flexibles. D’où la décision de faire en sorte que ses futures voitures produites se déplacent d’elles-mêmes dans l’usine. Une fois les pièces assemblées sur chaque module et les trois sections combinées, la voiture avance toute seule. C’est ainsi que les sièges et d’autres composants peuvent être montés avant que le toit et les panneaux latéraux ne soient fixés, ce qui simplifie la conception et les opérations des robots et autres équipements.
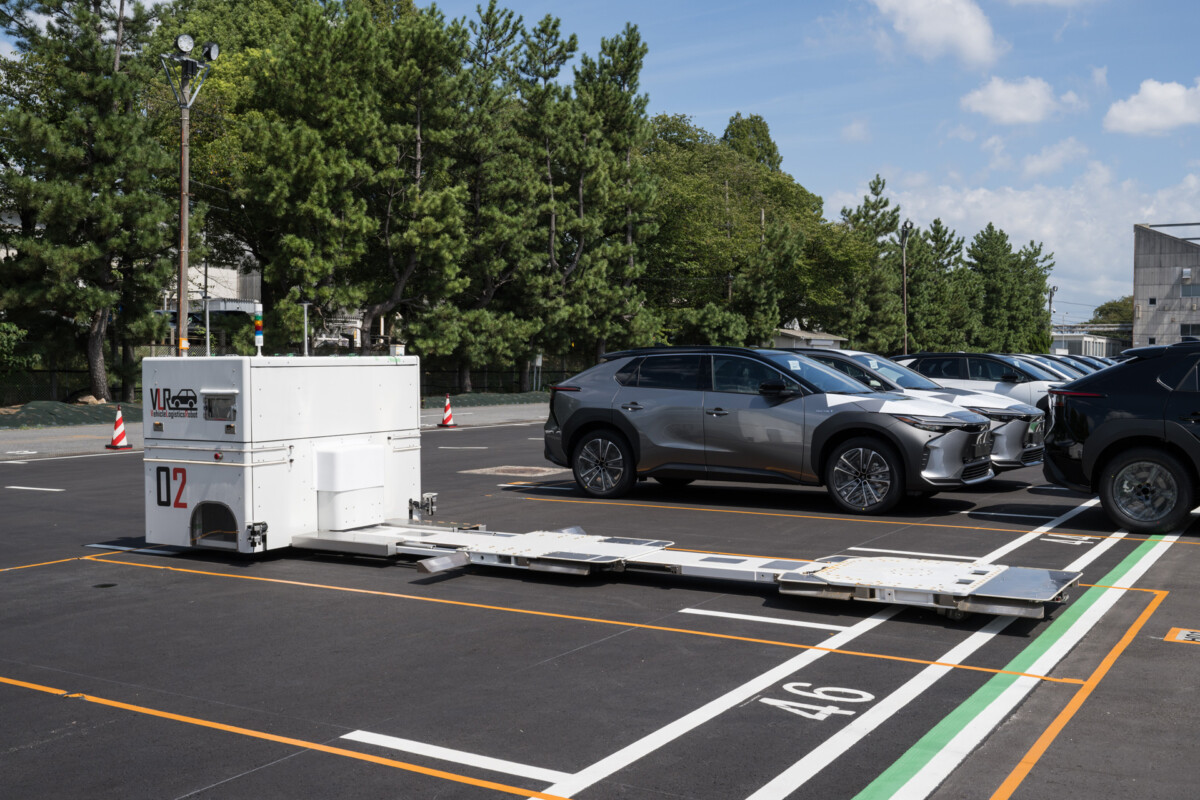
Ce qui est fou, c’est que cette ligne d’assemblage automotrice utilise les technologies de contrôle des véhicules et les capteurs qui servent à la voiture dans le cadre de la conduite autonome ! Des voitures autonomes, donc avant même d’être sur la route et qui roulent à une vitesse de 0,36 km/h. Des caméras réparties dans toute l’usine suivent les voitures et les maintiennent en mouvement le long de l’itinéraire.
Enfin, même la voiture finie, il n’y aura pas plus de conducteur humain pour l’emmener hors de l’usine, sur le parking extérieur d’où elle partira pour le monde entier. Des flottes de robots s’en chargeront en se glissant sous la voiture et en la soulevant jusqu’à la charger sur un camion. Toyota explique pouvoir remplacer 22 humains par 10 robots.
Téléchargez notre application Android et iOS ! Vous pourrez y lire nos articles, dossiers, et regarder nos dernières vidéos YouTube.
Ce contenu est bloqué car vous n'avez pas accepté les cookies et autres traceurs. Ce contenu est fourni par Disqus.
Pour pouvoir le visualiser, vous devez accepter l'usage étant opéré par Disqus avec vos données qui pourront être utilisées pour les finalités suivantes : vous permettre de visualiser et de partager des contenus avec des médias sociaux, favoriser le développement et l'amélioration des produits d'Humanoid et de ses partenaires, vous afficher des publicités personnalisées par rapport à votre profil et activité, vous définir un profil publicitaire personnalisé, mesurer la performance des publicités et du contenu de ce site et mesurer l'audience de ce site (en savoir plus)
En cliquant sur « J’accepte tout », vous consentez aux finalités susmentionnées pour l’ensemble des cookies et autres traceurs déposés par Humanoid et ses partenaires.
Vous gardez la possibilité de retirer votre consentement à tout moment. Pour plus d’informations, nous vous invitons à prendre connaissance de notre Politique cookies.
Gérer mes choix